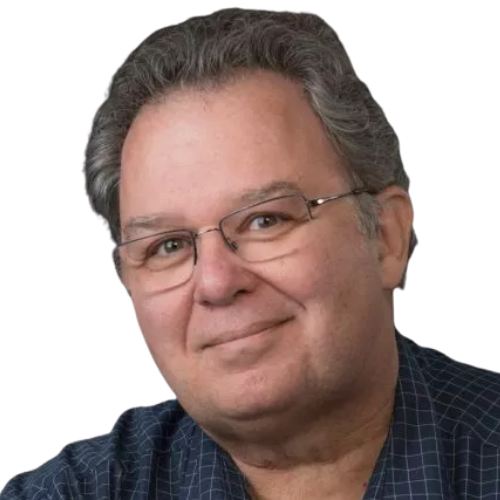
Roger has 30+ years of experience helping businesses to improve their processes. He has comprehensive operations leadership, assessment, and improvement skills to help organizations quickly improve their operations. He has extensive experience in plastics, paper/film converting, and assembly-based manufacturing in multiple industrial settings.
Roger led a team for five years in the design and manufacture of custom machinery that supports lean manufacturing. He has led and participated in over 350 Kaizen events and led numerous 3P and Design for Manufacture events. He also has excellent VSM, engineering and fixture design skills. From overall plant layout to tool locations at a workstation, Roger links customer demand to existing process and demonstrates how to convert to a lean manufacturing approach.
Doubled productivity of a converting line by leveraging assessment insights into an implementation plan.
Dramatically improved output per labor hour by 70%+, on-time delivery of 98%+, lead times of less than two (2) weeks. Custom fixture design and build for an assembly line – enabled line to run in a mixed model mode which improved on-time delivery, reduced lead times and reduced on-hand inventories.
Improved layout and flow of assembly lines; Installed “kanban” systems for raw and WIP materials; 5S of entire facilities; Set up reduction events on many different types of equipment; Numerous custom fixturing/dedicated equipment designs specific to a product line.
Has led 100’s of VSM events leading to significantly improved future states. Developed electronic VSM modeling tool for quickly evaluating various scenarios from changes in demand (takt) to improved operational effectiveness.
Developed electronic model for evaluating various cell designs based on task analysis, takt and cycle times, number of operations, people and equipment.