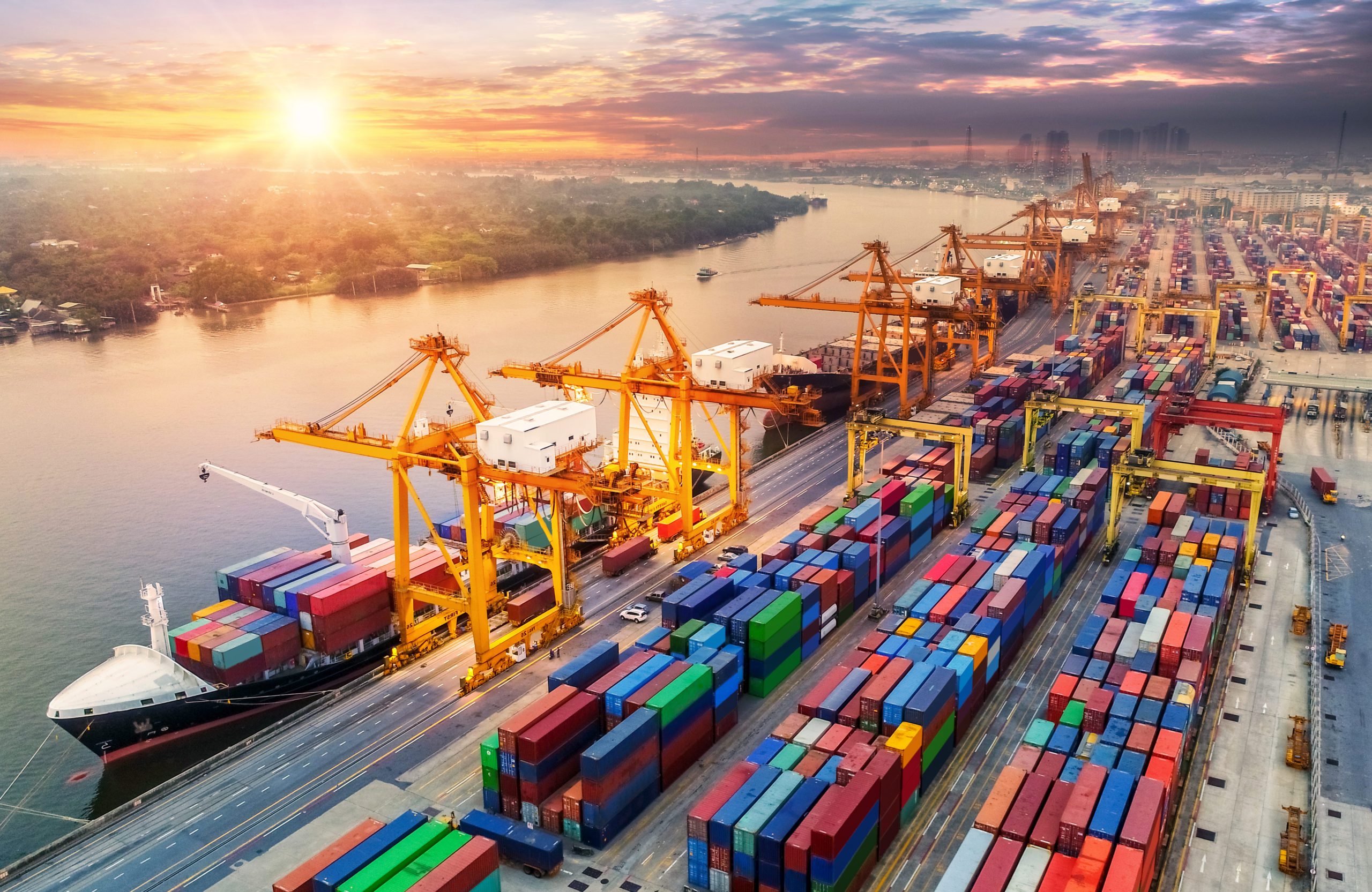
Breaking Down JIT and the Supply Chain Crisis
Quite a few supply-chain strategies were developed throughout the years using the famous nostrum, “All other things being equal, we should use the method that costs the least.” This worked well for a long time, but now we are in a situation where the expectation that conditions would remain equal may no longer be valid. Key among these is JIT (Just-in-Time) inventory and supply-chain management.
This article reviews key elements of the supply chain and JIT theory, and outlines how businesses are coping with recent COVID-19 disruptions to the supply chain. Do business leaders think recent conditions will persist long enough to require a new supply chain model? Or is this a temporary situation that will soon be restored to the successful performance of our pre-COVID supply chains?
Started in Japan in the 1950’s and led by Toyota and others, JIT has been successfully adopted in the U.S. by most major manufacturers including GM, Ford, Harley Davidson, Dell and Hewlett Packard. In theory, the JIT process is meant to reduce waste by minimizing inventory, product handling and the associated carrying costs such as warehousing. It ensures that only what is needed is provided within a very narrow logistics window. By reducing inventory at each step of the production process, companies can minimize capital investment and ensure more efficient conversion of raw material into finished parts.
The stability of the supply chain has made JIT a highly successful approach for the past few decades. However, many believe that the reliance on JIT has bordered on obsessive, especially in an era of low interest rates which reduce the financial benefit of minimizing inventory. To be effective, JIT requires producers to forecast demand accurately, and it relies on steady production, high-quality workmanship, minimal machine breakdowns and reliable suppliers. If these variables changes, the savings can be eliminated and the supply chain disrupted.
Along Came the Disruptor: COVID-19
With lockdowns, quarantines, social distancing and skeletal staffing, the benefits of JIT began to fizzle in the face of the pandemic. JIT was intended to foster supply chain flexibility but has revealed a level of fragility as key suppliers have come under strain, which has led to the loss of speed and nimbleness.
“The reality is that legacy transportation technology and the limitation of traditional supply chain practices are no longer enough to keep pace with the market,” says Bill Driegert, Head of Operations, Uber Freight.
Toilet paper shortages, seriously? Yes, the retail model of reduced store level stocks, combined with increased orders to suppliers, exposed major flaws to the system. Suppliers were unable to keep up with this sudden volatility.
“Just-in-time (JIT) inventory policies account for optimistic levels of demand and supply variations and were rendered suboptimal during the initial panic buying phase,” explains Rajesh Shetty, Associate Director at Boston Consulting Group (BCG). However, even standard risk management methods would not have prepared supply chains for extreme volatility from black-swan type events, but the reliance on aggressive JIT models clearly exposed companies to additional performance degradation.”
Adjustments to Improve the Supply Chain
- Increase Supply Chain Technology: There is already an increased focus in leveraging technology to reduce risks and improve management of supply chains. “In many ways, the widespread impact of COVID-19 has been a forcing-function for innovation, and shippers for whom digital transformation wasn’t a top priority are suddenly moving quickly,” says Driegert. “We anticipate a spike in supply chain technologies in response to the pandemic,” agrees Shetty. “End-to-end supply chain planning systems including control tower solutions, inventory optimization tools and advanced analytics will be able to mitigate some of the risks associated with JIT while balancing the service-cost trade-offs.”
- Increase Inventory: Companies will consider increasing inventory levels (at least to some degree) to spread risk more effectively and have back-up suppliers at the ready. This will likely lead to increased cost due to lower volume discounts; however, this may be a more financially sound decision when the alternative is the inability to satisfy customer needs.
- Re-evaluate Geographic Sourcing: Companies will rethink where they source their materials and the related vulnerabilities. With continued uncertainty of delivery times, sourcing supplies closer to the factory may become a stronger consideration, whether that means moving supplies from the far east to closer low-cost countries, or simply looking for suppliers within your home state.
Also, while there have always been different tax and environmental regulations specific to various U.S. jurisdictions, these will likely impact more business decisions than before. For example, if California ports cannot or will not unload ships at the pace you desire, but Florida ports can and will, this will make a difference in a company’s supply chain decision-making.
BDO, the consulting firm, urged manufacturers to reevaluate their JIT inventory strategies and consider developing alternative sources of supplies or stockpiles of critical materials or products. “The manufacturing industry is at a crossroads,” BDO says in a report released in 2020. “On one end are the continued headwinds that manufacturers will face due to the pandemic recession. On the other are emerging opportunities for growth and innovation that organizations cannot afford to ignore. The future will be a balancing act between mitigating risk, navigating continued uncertainty and seizing new opportunities.”
Also, the seven drivers of “Partnering for Production” defined by James H. Greene in the Production & Inventory Control Handbook still apply:
- QUALITY – zero defects and good work processes
- TIMELINESS – zero days early and zero days late, requires complete control of the entire product delivery cycle
- COMMUNICATIONS – careful and thorough sharing of information vital for all partners to perform well in the partnership; next to trust, this is the biggest challenge facing would-be partners
- FLEXIBILITY – willingness and ability to meet new market opportunities
- ATTITUDE OF CONTINUOUS IMPROVEMENT – teams, openness to new ideas, and willingness to try new production approaches
- HABIT OF COOPERATION – internal teams, industry consortia, training and assistance for suppliers
- TRUST – although trust is the “fuzziest” term, it is easy to identify actions that destroy trust
JIT is Here to Stay
As long as cost continues to be a key business driver, JIT isn’t going away. There simply isn’t enough margin to eliminate JIT and its overall efficiency. When the new business-as-usual is established, JIT will still outcompete other supply chain models. While massive inventory buffers aren’t going to make a return, companies will make adjustments to increase stock levels, leverage more technology-driven inventory management solutions, and make geographic adjustments. These things, along with close collaboration between suppliers, customers and their end markets, will remain imperative to ensure an ongoing, cost-effective supply of goods…Just in time.